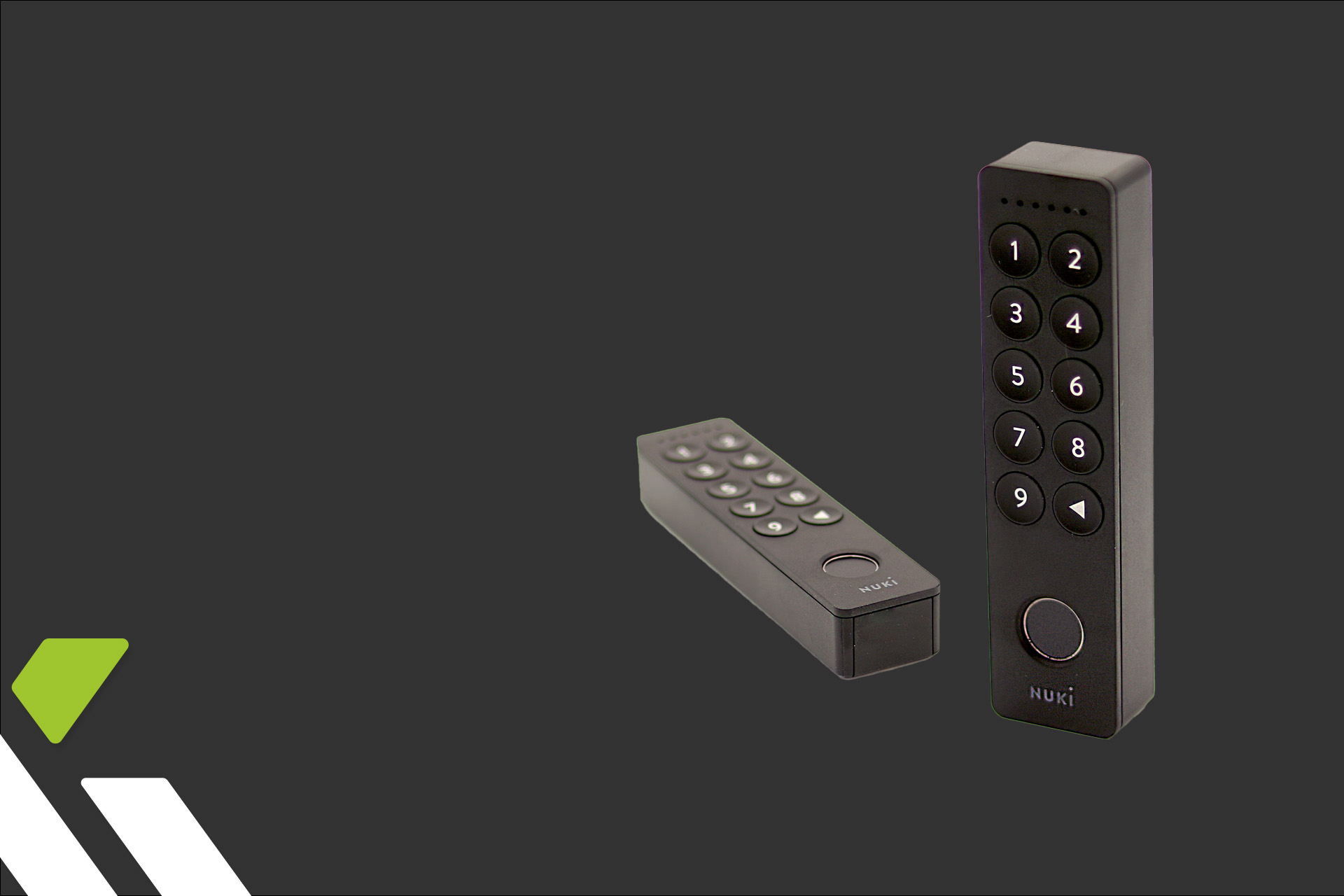
Insights into development: the Keypad 2.0 from Nuki
From the initial concept to the finished premium product for end customers: Nuki Home Solutions GmbH, based in Graz, is a pioneer and European market leader in smart locks. With the electronic door lock, the physical key is a thing of the past. From now on, you can go through life with one less thing to worry about and still have your door under control at all times – a clear conscience, full control and certified security included. With the new Keypad 2.0, you can now open your door faster than ever before: simply with your finger.
The Keypad 2.0 is therefore the perfect accessory for the Nuki Smart Lock. In addition, the Keypad 2.0 offers customers simple installation and a high level of user-friendliness. By using fingerprint technology or by entering a 6-digit access code, you can open your door in a matter of seconds. The Nuki Keypad 2.0 has been available on the market since November 2022. The high-quality end product that customers can now hold in their hands is the result of a great collaboration and successful project implementation between us and Nuki Home Solutions GmbH.
It all started with an initial request to us to develop a keypad. The focus was on the premium quality and high functionality of the new product. Customers should be able to immediately perceive the high quality and precision of the product through its aesthetics and feel. A well thought-out core and smart technology combined with a pleasant feel should result in an appealing and modern shape. After all, the product attached to the external façade must not only be visually appealing, but also functional. With the initial order specifications, we moved on to the basic design phase following a cost estimate. It is particularly important to us to involve the customer in the project implementation as transparently and clearly as possible right from the start. Ongoing coordination with Nuki was therefore an important basis for the successful implementation of the Keypad 2.0.
In prototype production, we rely on our in-house production technologies in the field of 3D printing to perfect the production of individual components. The prototyping phase made it possible to check the functionality of the product and adapt it if necessary. The main focus is always on the interaction of the individual components and the development of a suitable manufacturing process for our customers, in this case for the special requirements of the Keypad 2.0. Here, for example, the space conditions were very tight, requiring extensive functionality in a small installation space. This posed a challenge not only for component design, but also for tolerance management.
Following a successful concept phase, planning for series production was initiated together with Nuki. The series design included plastic injection-molded parts, stamped parts and stamped-bent parts as well as a silicone casting. Each component underwent a failure mode and effects analysis in order to determine the specific component requirements and develop a final concept for assembly. In a so-called DFM phase (“design for manufacturing”), the next step was to coordinate with the component suppliers before series production could be initiated. All properties were thoroughly examined in an initial sampling of the components and a functional test: For example, the snap-in of the mounting plate catch, the pressure points of the buttons or the opening of the battery cover were closely scrutinized. Another important factor was the “IP54 protection class” – the Keypad 2.0 must be protected against splash water and ensure that it remains completely dustproof. Features that we have made possible through ongoing testing and improvements. To ensure the high product quality of the Keypad 2.0, there were also change loops and re-sampling of the components during this phase. Only when all the requirements had been met did we start the pre-series with assembly by a contract manufacturer. This was followed by further test runs with the fully assembled Keypad 2.0. These include, for example, a drop test from a height of 1.2 m, a leak test to IP54, tests in a climatic chamber or the service life test of the buttons.
Based on the results of these tests, we were able to create a precise package of measures to bring the components into pre-series in an improved form. With the successful completion of the pre-series phase, the Nuki Keypad 2.0 has been released for final series production. The Nuki Keypad 2.0 was officially launched at the end of 2022 – and we can look back on a successful project implementation.